Oasis
Matt and I started a small ceramic project in mid-2020 to send home to you all as a gift. As the Covid-19 situation dragged on (along with getting side tracked with other business programs), what started as a small project just seemed to get bigger as time went on.
Anyway, hope you enjoy them for whatever purpose you find. Originally they were designed to be birdbaths but generally its up to you if you’d like to use them that way.
Heres a bit of process and a little more background on how this came together- This is more or less the design and thinking process for most of our projects, Enjoy!


Idea Development
This is the part of the process where we are trying to find the right design idea. What kind of object do we really want to make? What is the function of it? What is interesting or unique about it? What would we really be excited to spend a few months working on?
Its an exploration that is mostly just sketching, finding inspiration photos and possible uses for whatever it is that we are trying to create.
Concept Refinement
After the inital sketch and concepting phase and we established that ‘birdbath’ was the direction, we started into an iterative 3d phase working in our 3d modeling software to try to capture the sculptural design idea- alongside the reality that this thing must actually be able to be made somehow using traditional ceramic production methods which we don’t want to reinvent or challenge too much.



Production
Once we got the main idea together and finalized in 3D, we got in contact with a professional sculptor from our network and set up an area within his studio to work in Richmond, California.
For context, it’s about a 40 minute drive from Potrero Hill in San Francisco to Richmond.
We started in May 2020.
Toki Studio
The birdbaths ended up being kind of larger scale than we’d originally thought but ended up being perfect for working at Toki Studio as we needed the extra space and larger equipment.
John Toki is a revered ceramicist, author, educator and sculptor. John is well known in California for his monolithic, large-scale nature inspired sculptures, some of which are thousands of pounds and tens of feet high. Johns’ main kiln (first photo) is larger than some one bedroom apartments in San Francisco.
John helped us initially with the plaster mould making and giving us oversight on measurements, slip and firing temperatures. As these kinds of projects don’t come with an instruction manual, John was there to help us troubleshoot issues as they came up.


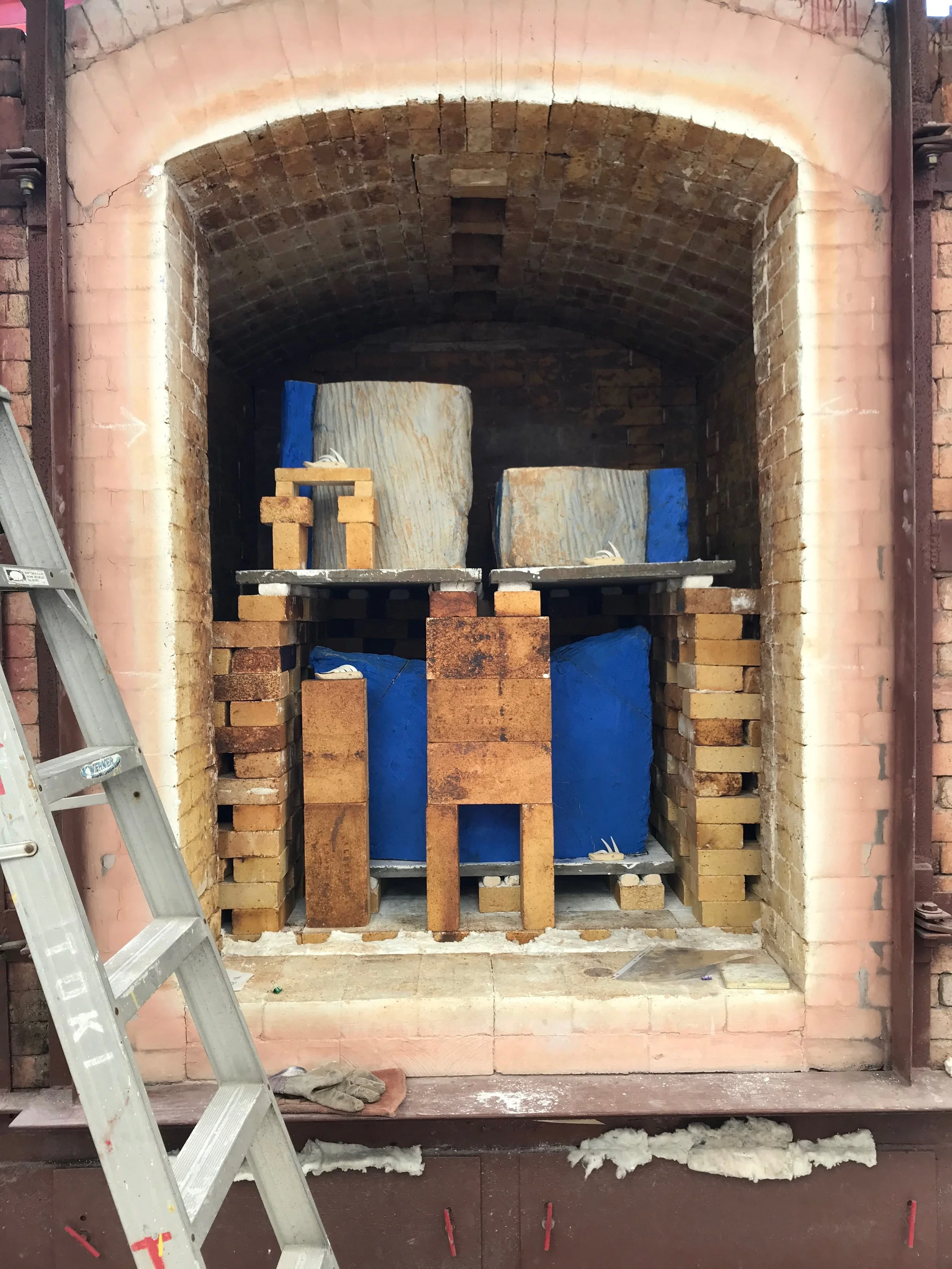
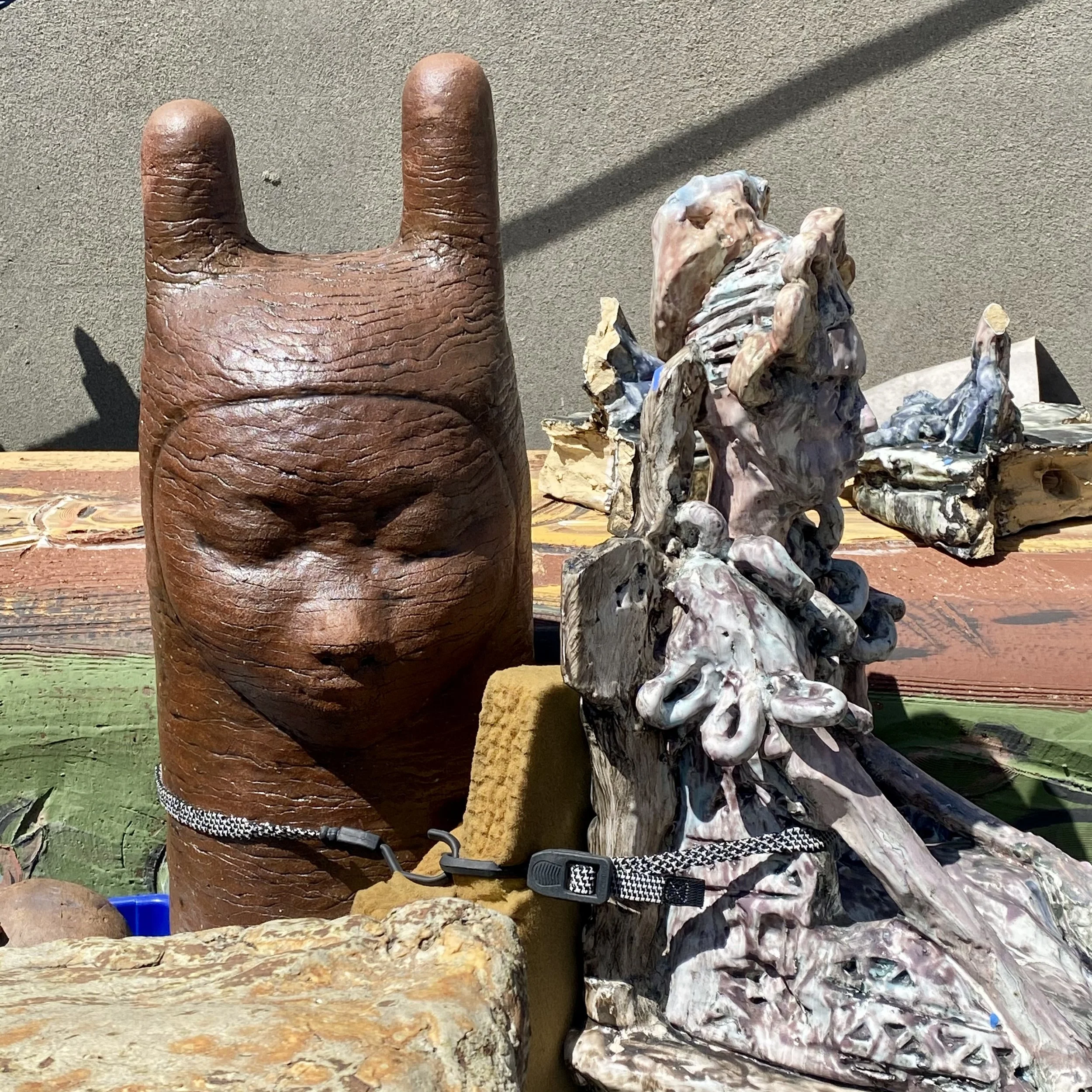
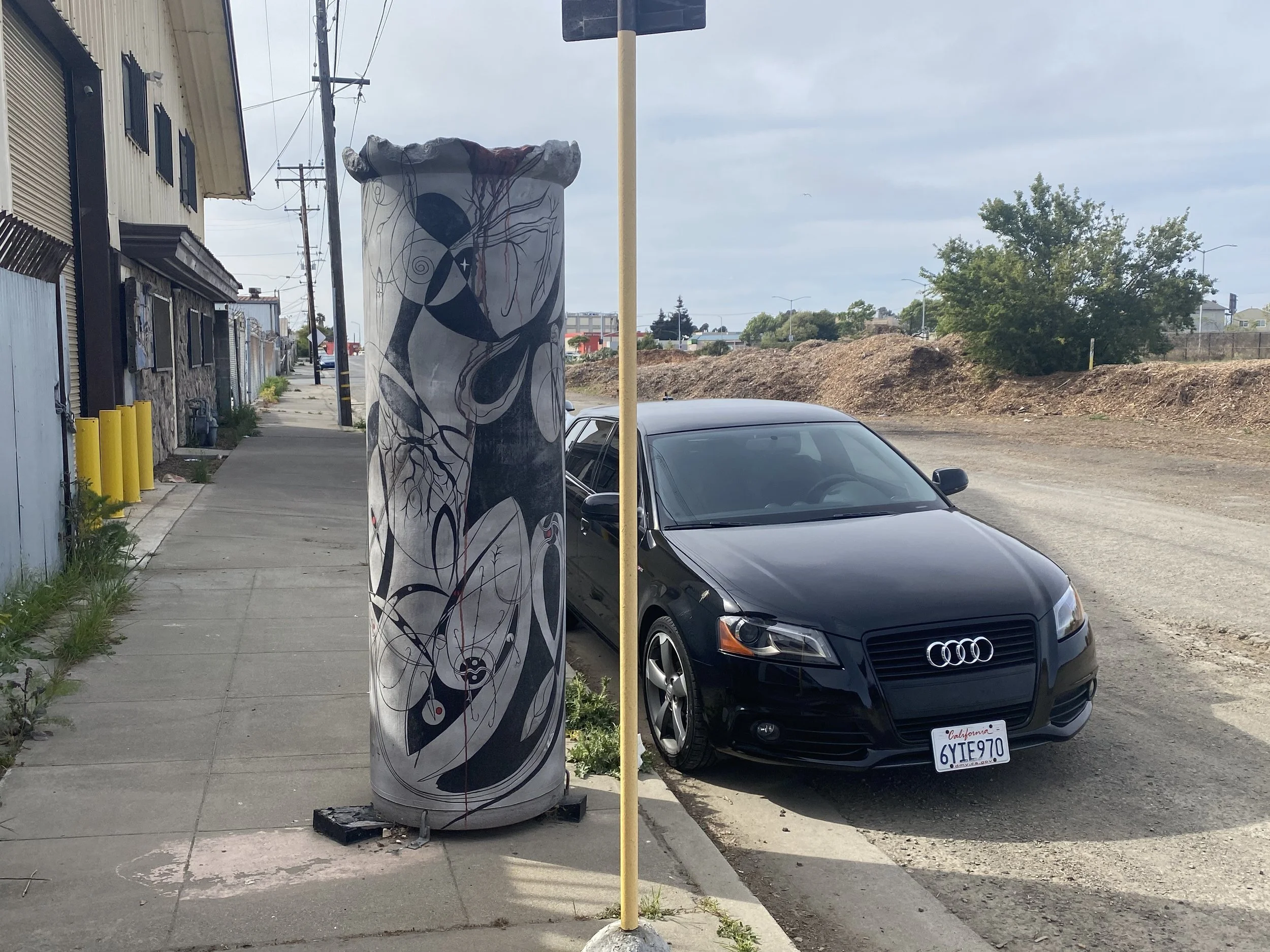
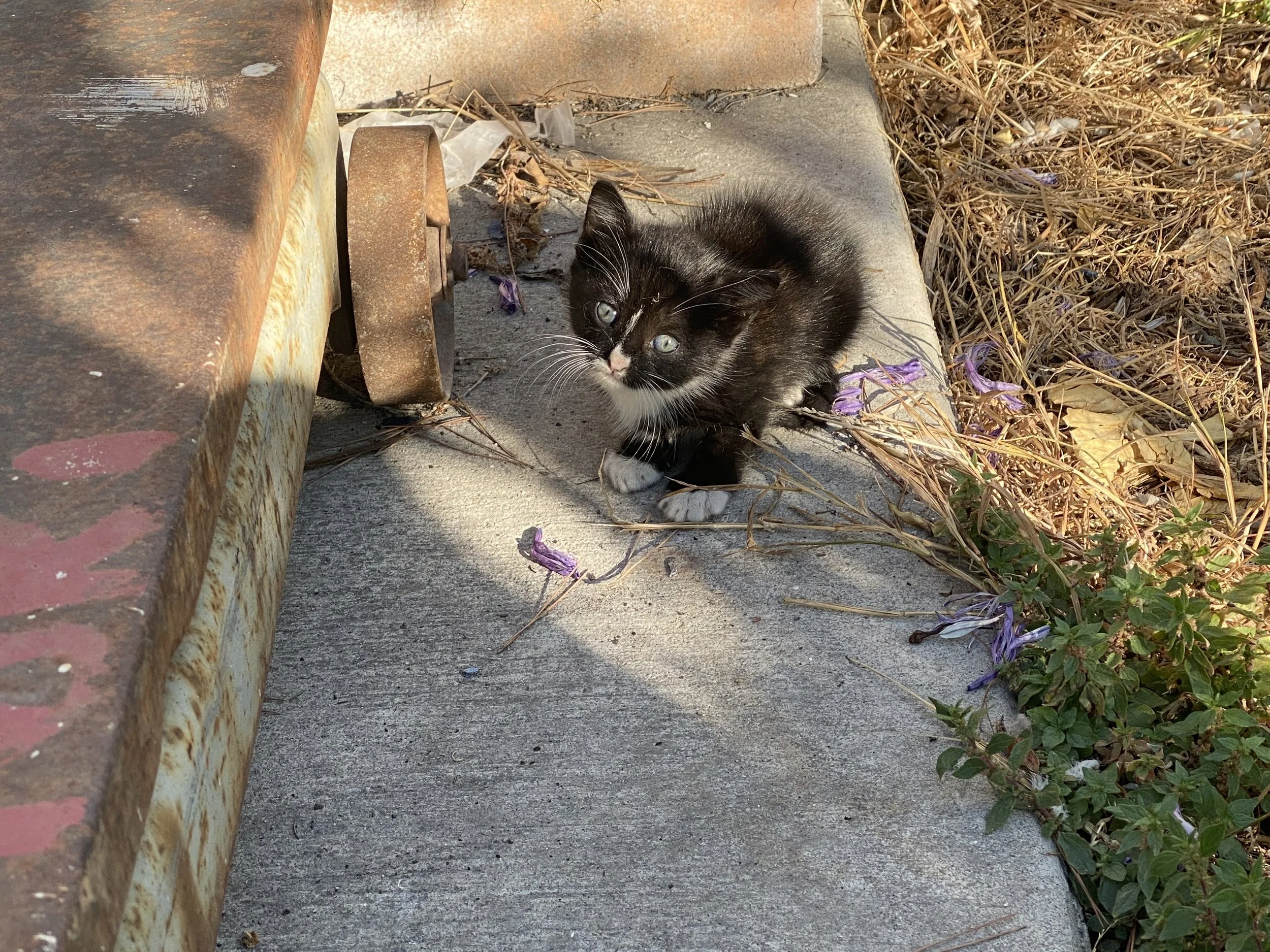





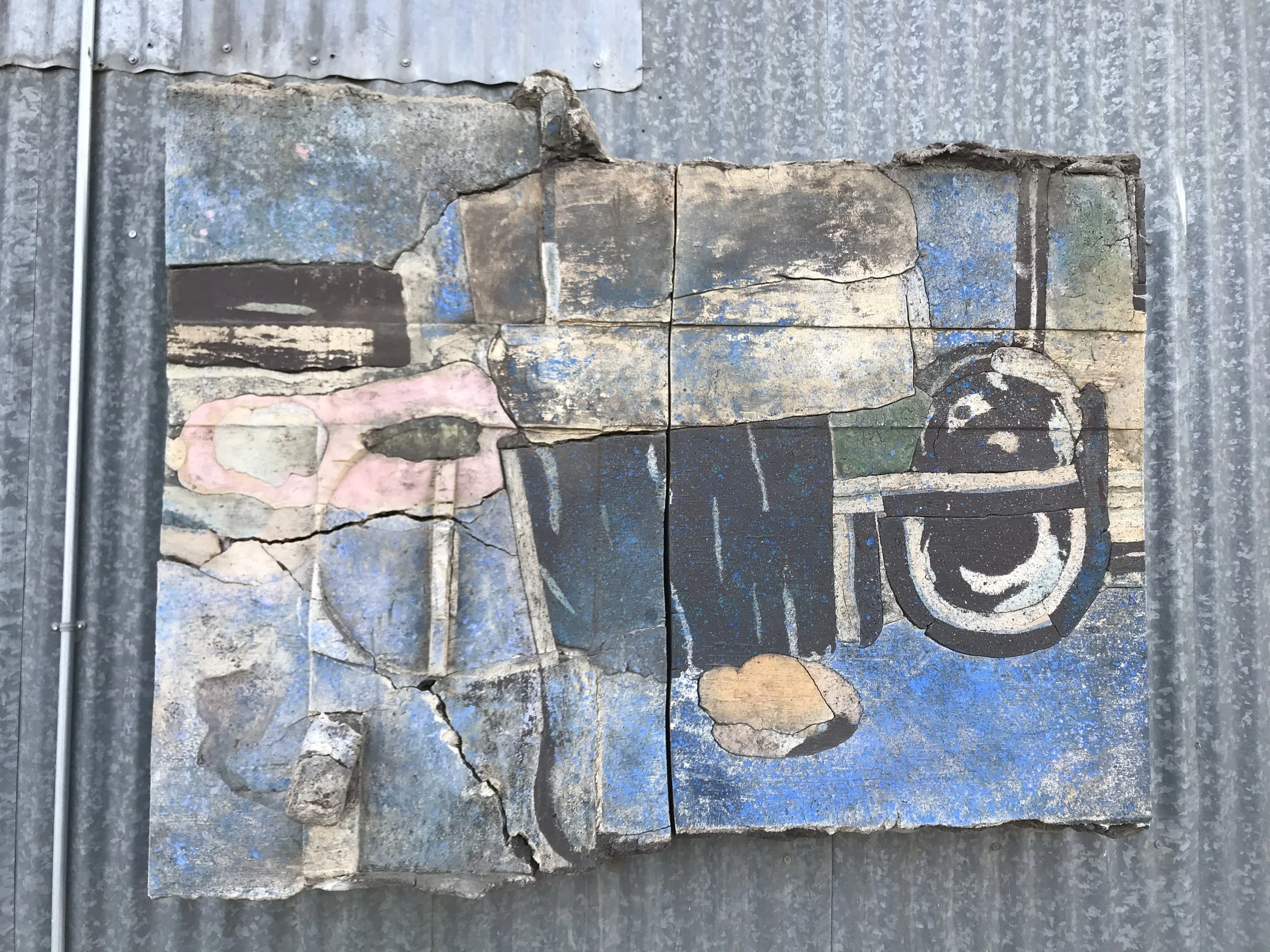

Richmond, California
Richmond is very different area than the rest of the East Bay. It’s kind of an industrial, manufacturing kind of city that unfortunately has a lot of homeless and can be pretty dangerous at night. Though we had to come to the studio many times after nightfall, the studio itself, food and other unique areas made up for how sketchy Richmond can be.
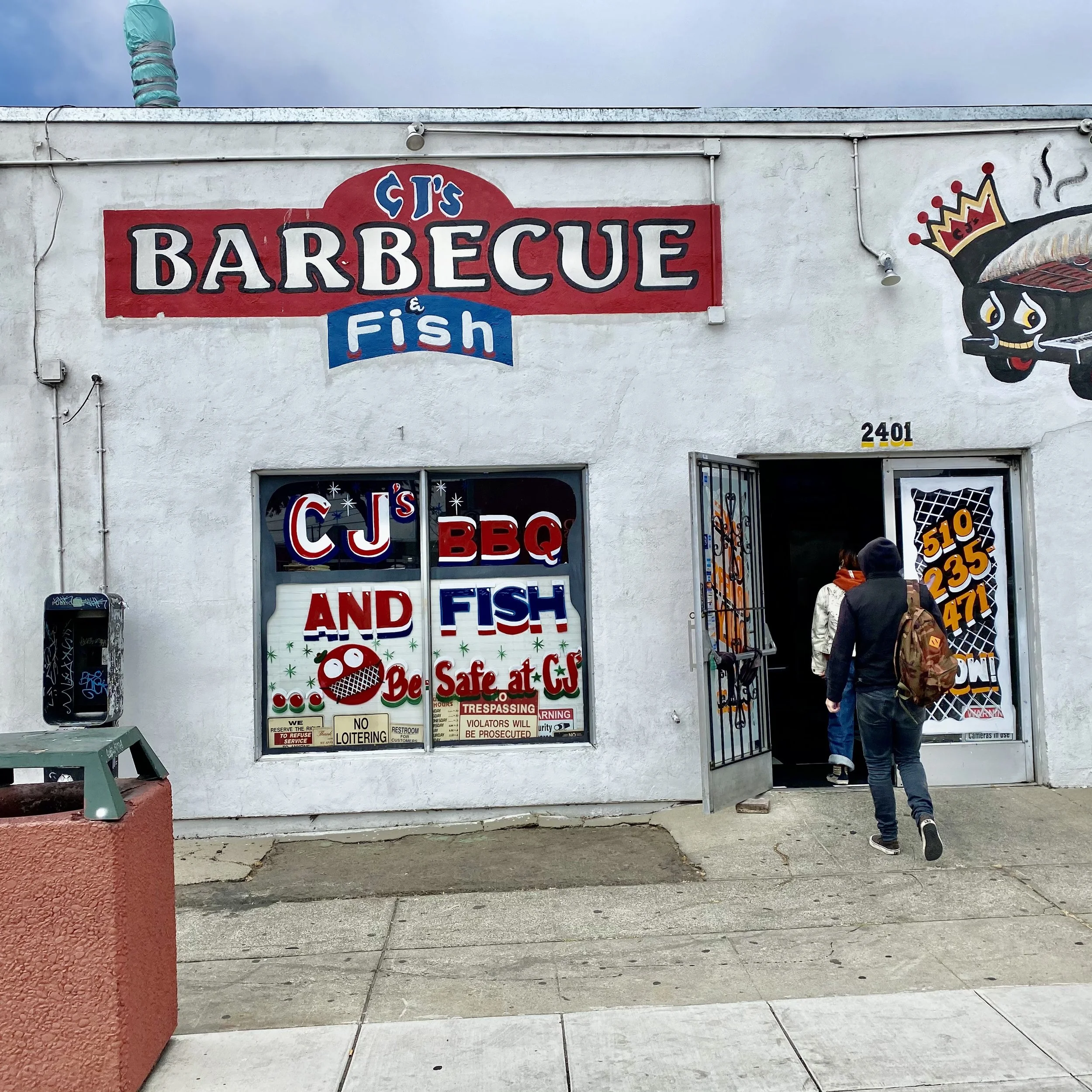
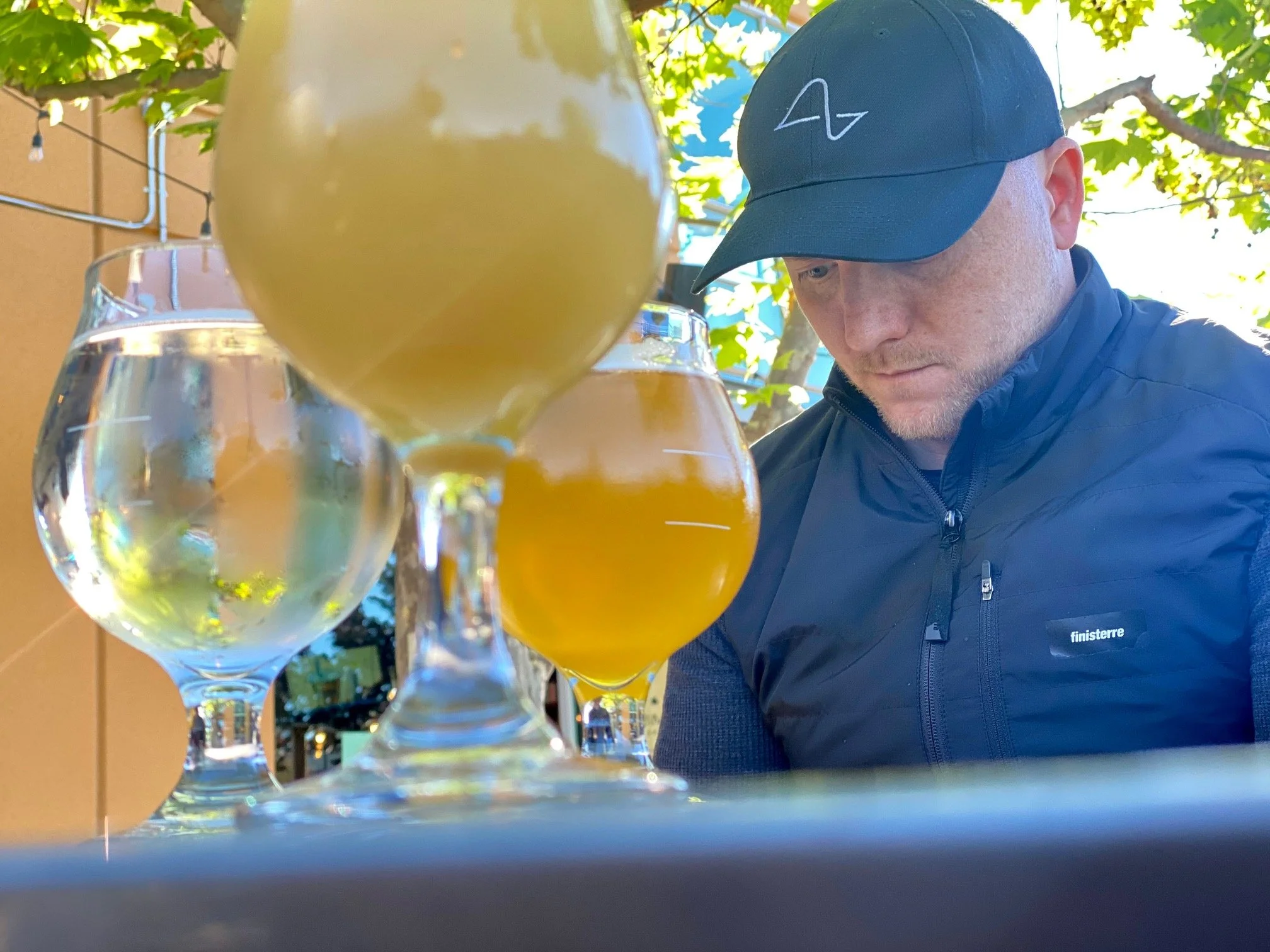

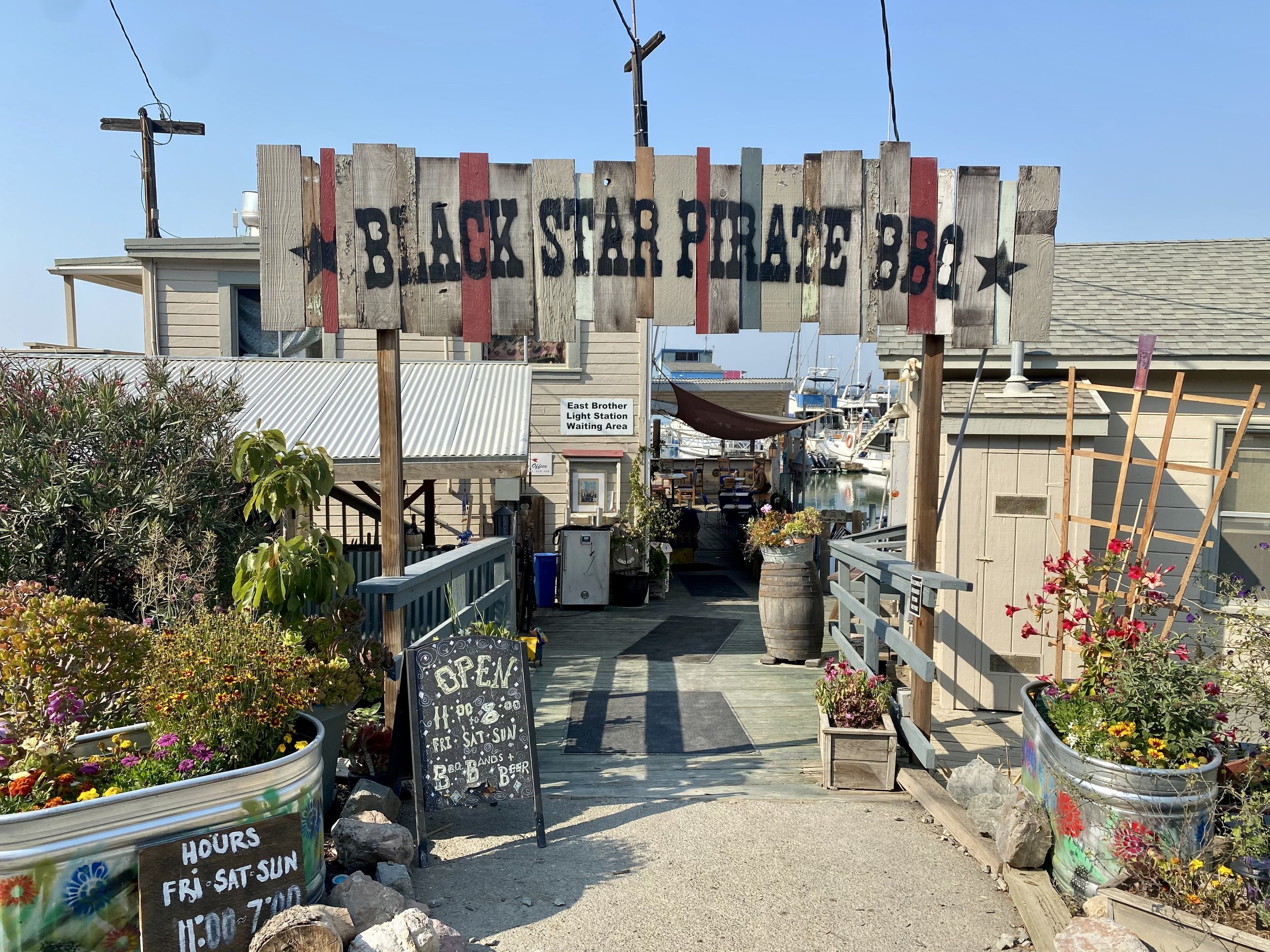
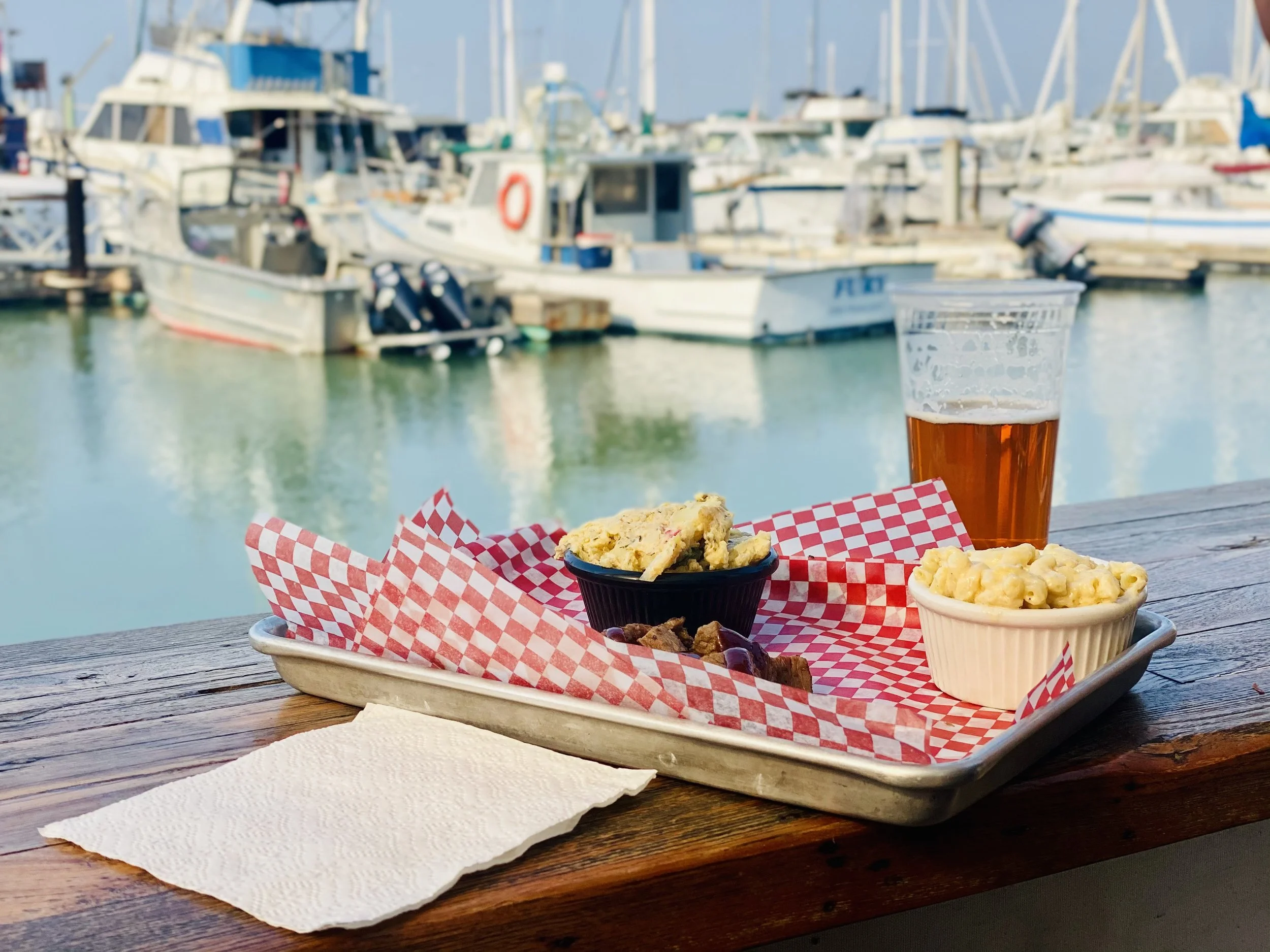





Mould Making
Process from the plaster casting and mould making around the birdbath buck.
The inner ‘original’ was a solid resin block that we had CNC’d in China.



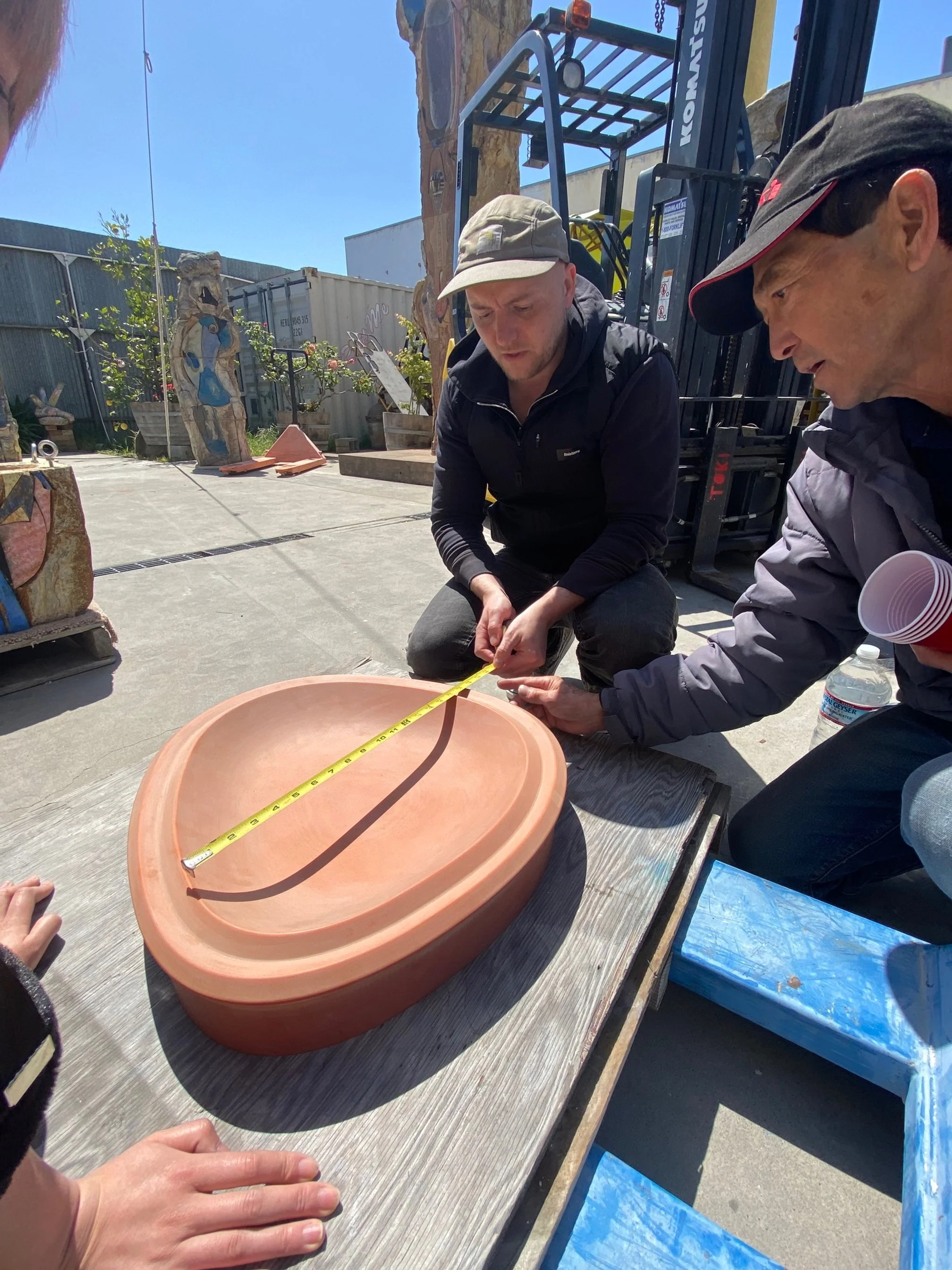
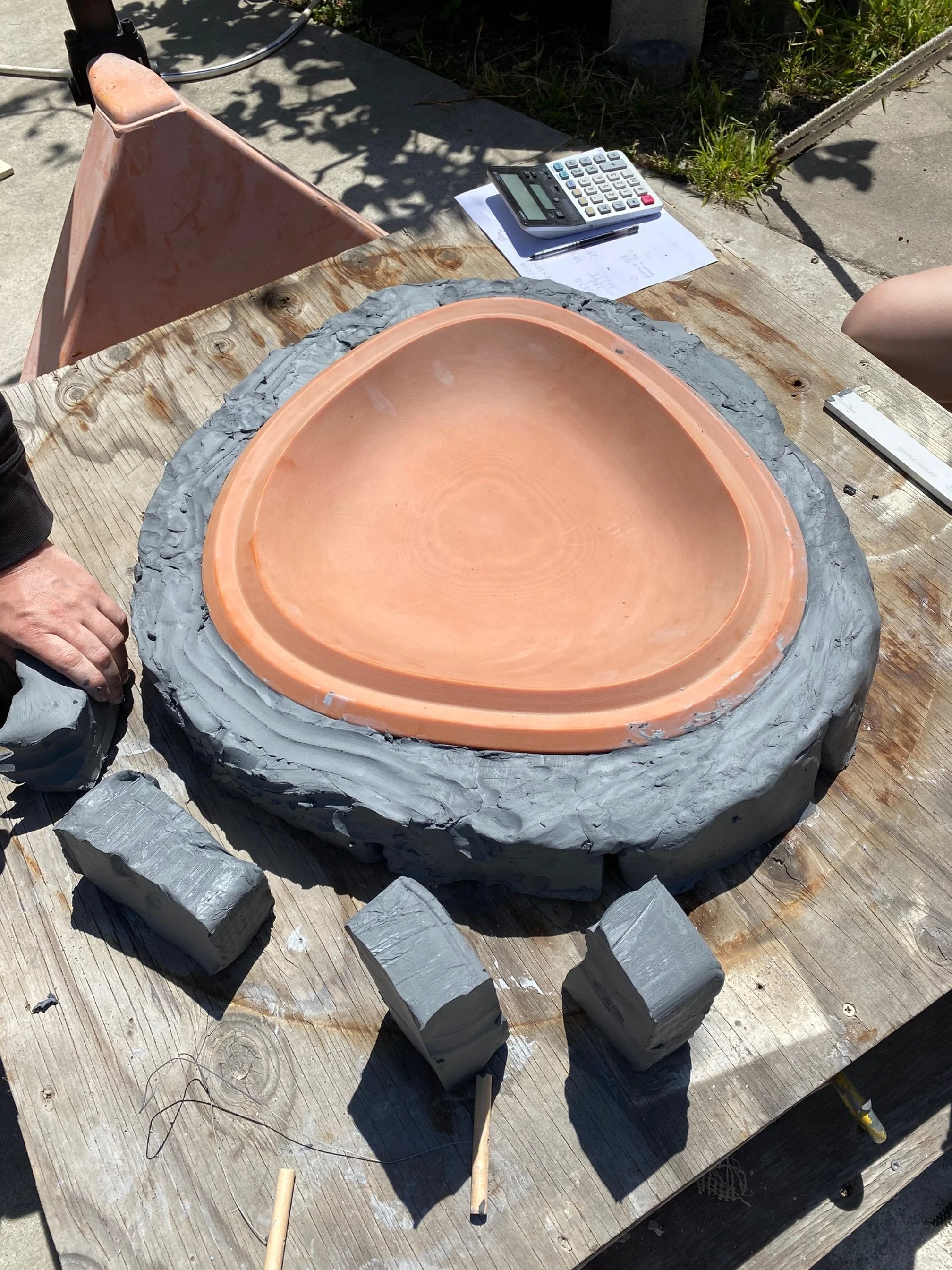


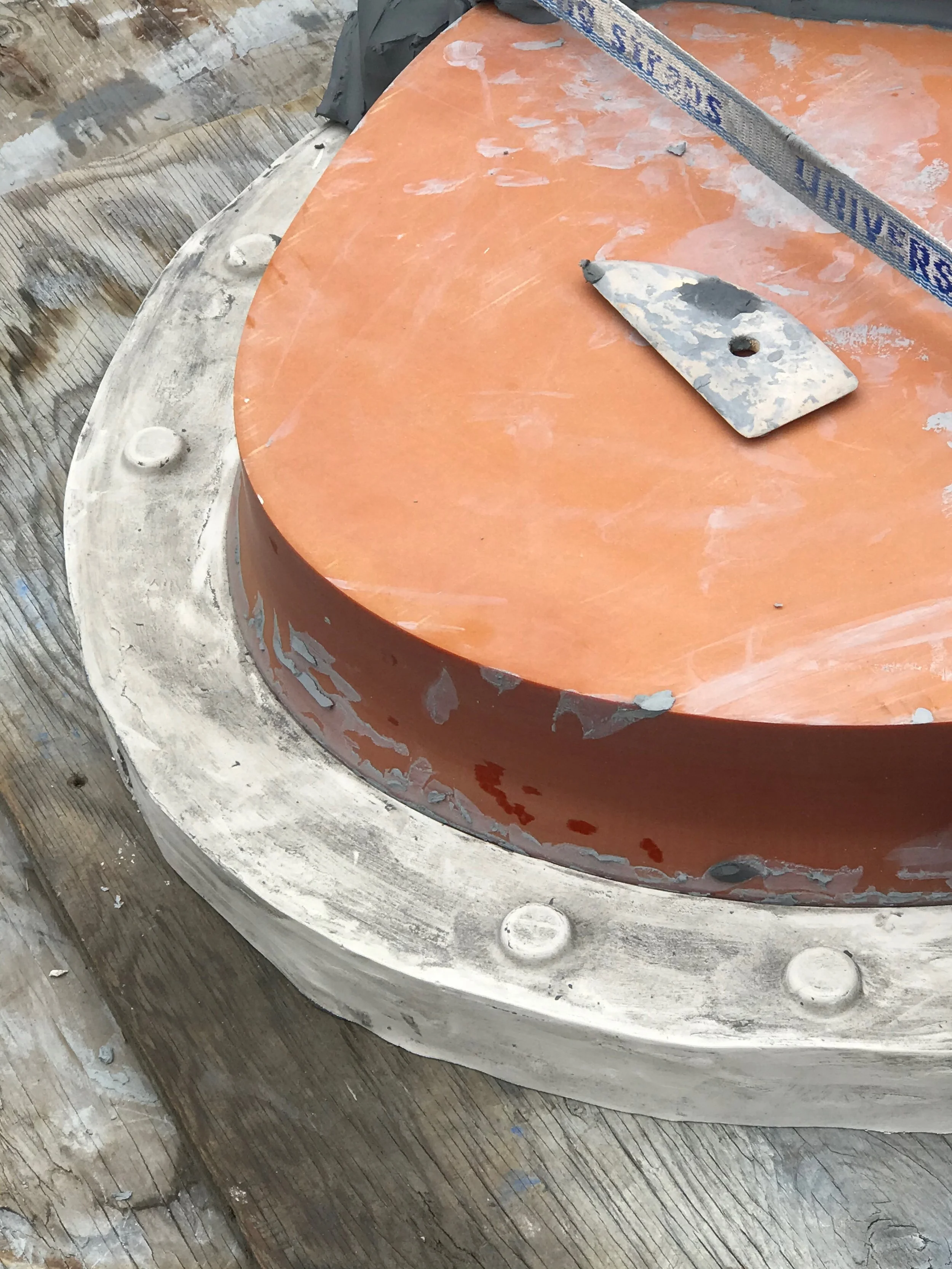

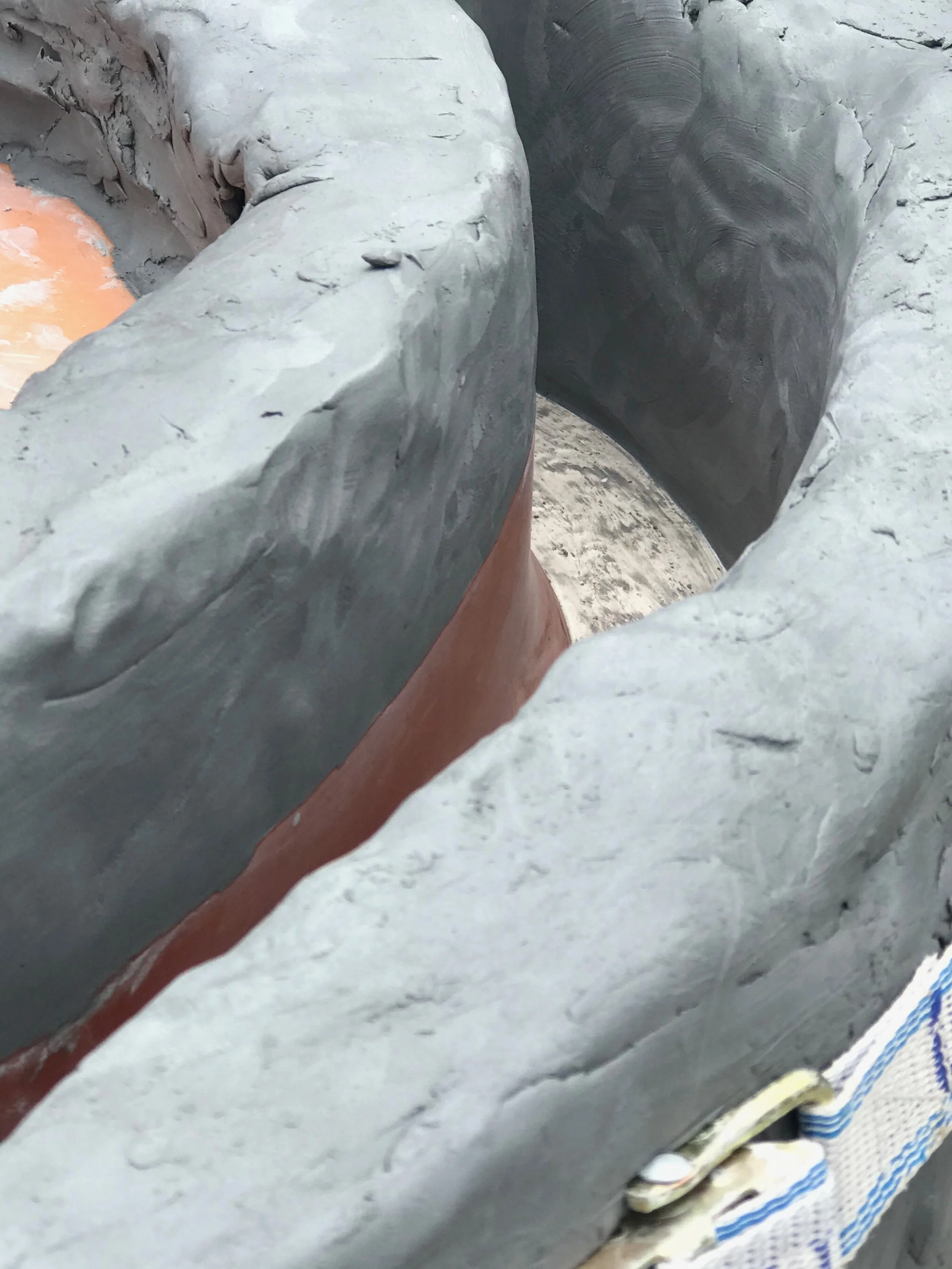







Pouring Slip
Some process from the pouring of the slip into the mould. The mould ended up being five parts (three walls and a top and a bottom). The mould was about 60lbs empty and 150lbs full. We had to come up with some creative ways to lift the mould to pour out the remaining slip about 1.5 hours after initially filling it up for each birdbath.


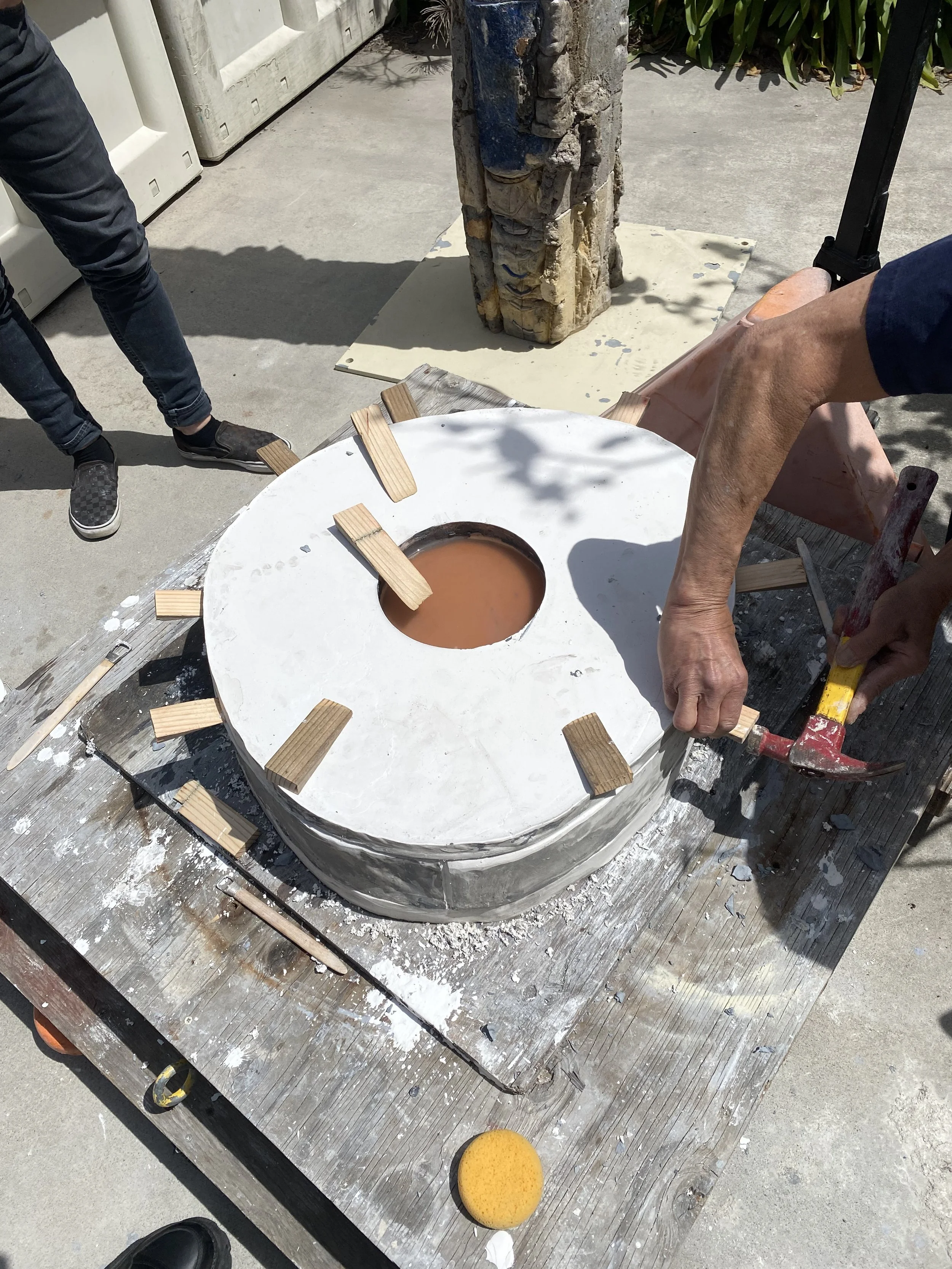
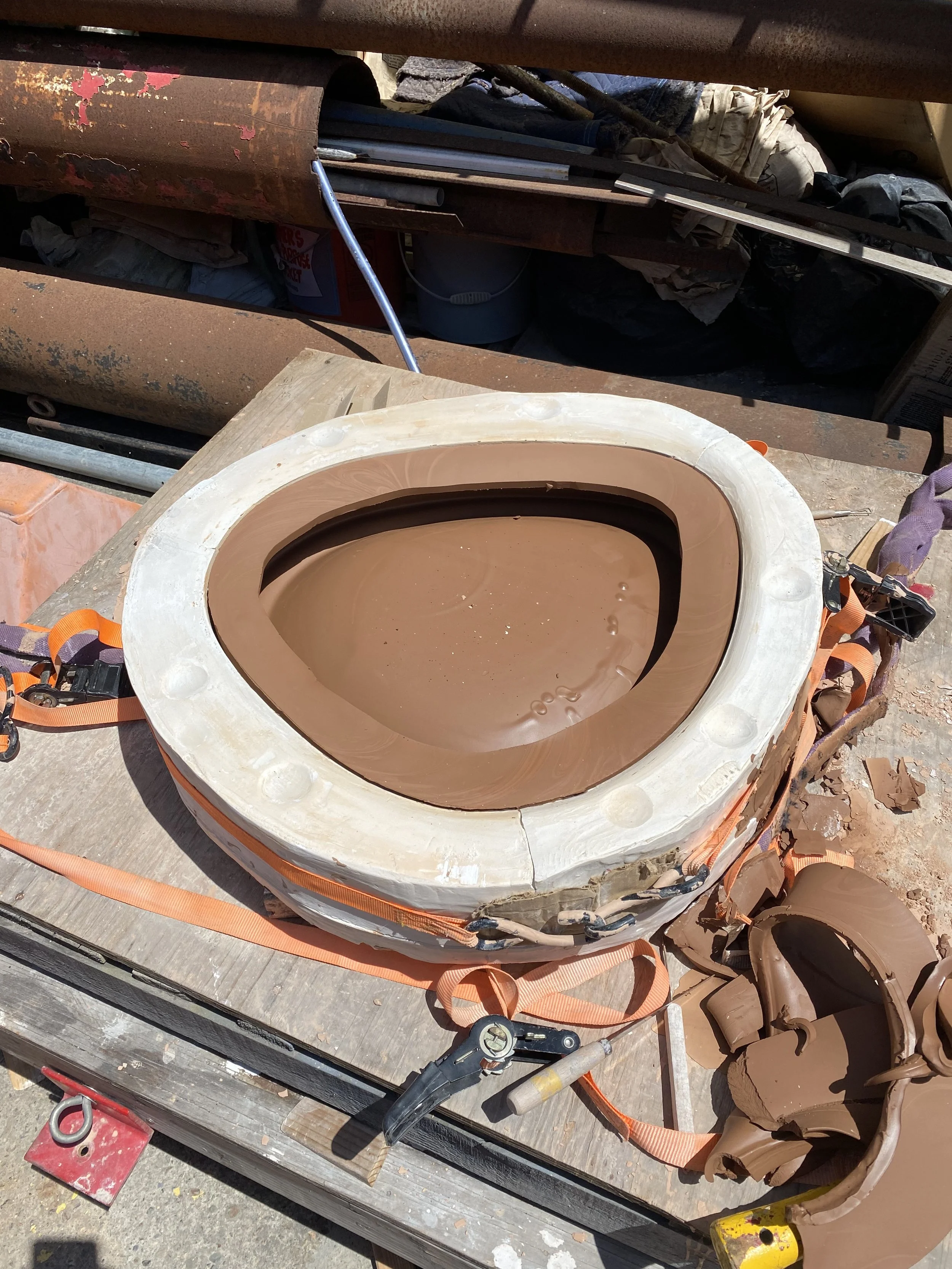



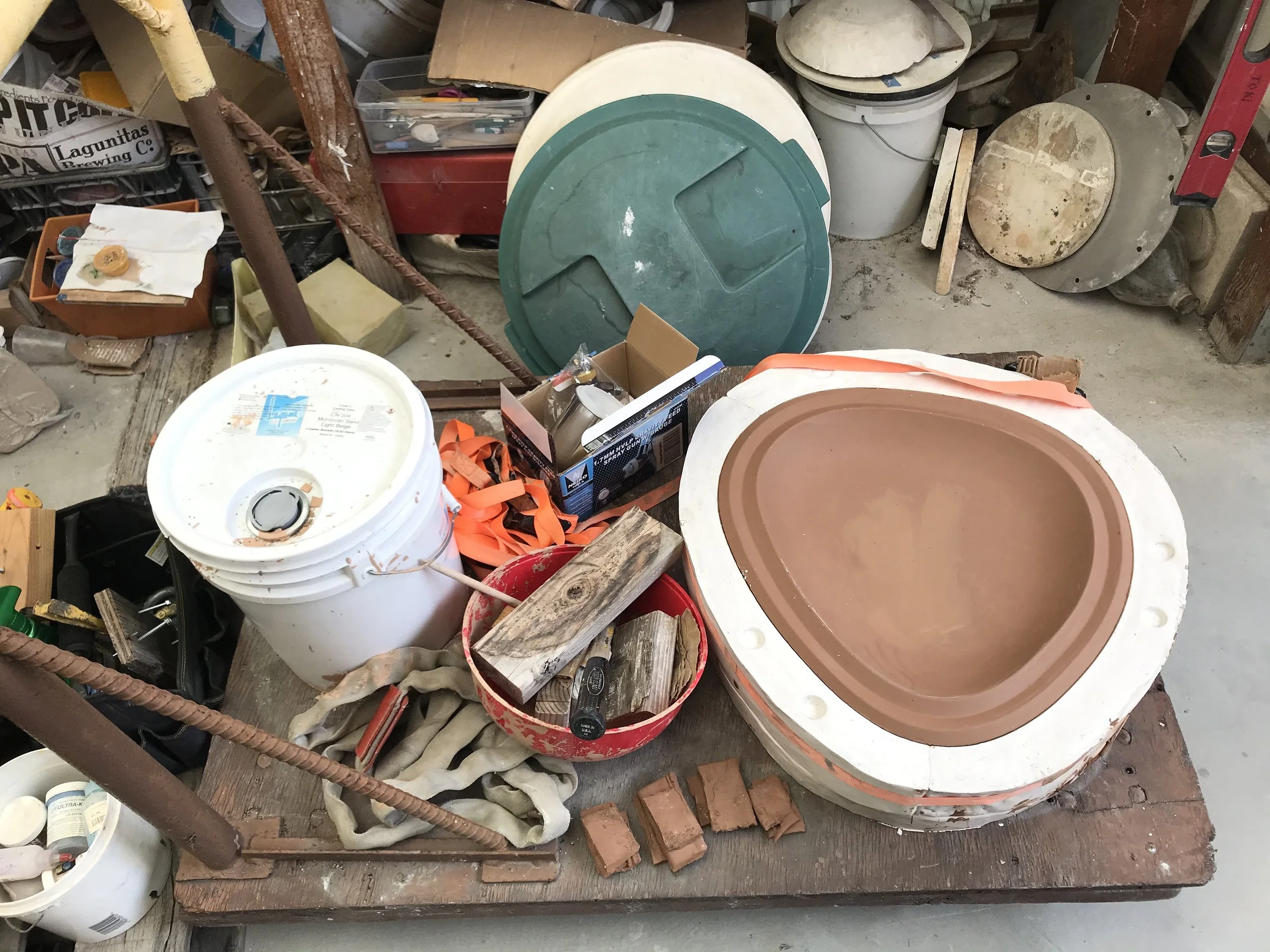

Bisque Firing
Snapshots of the first firing. We got about 12 good ones out of the 30 gallons of slip we had.

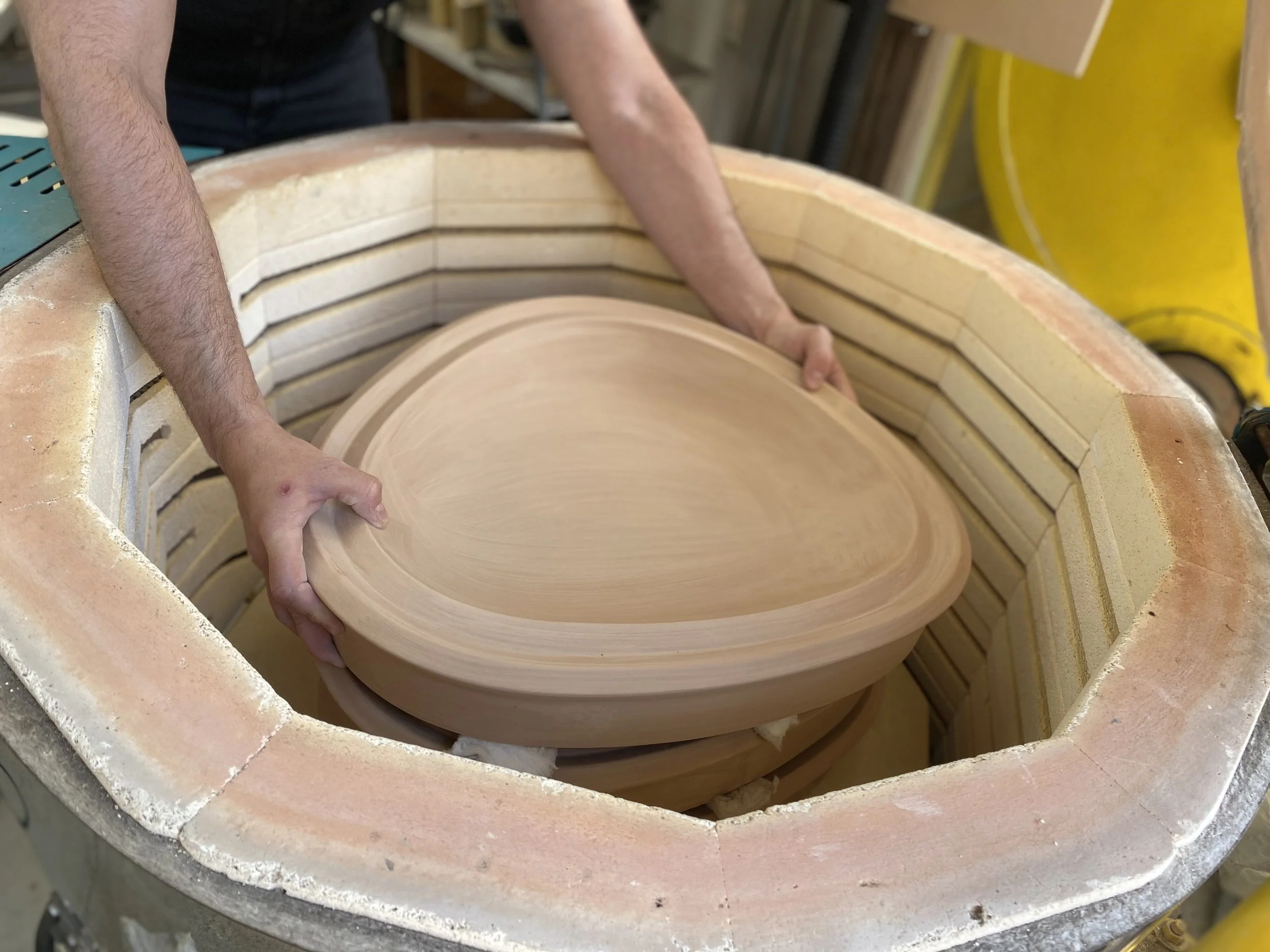
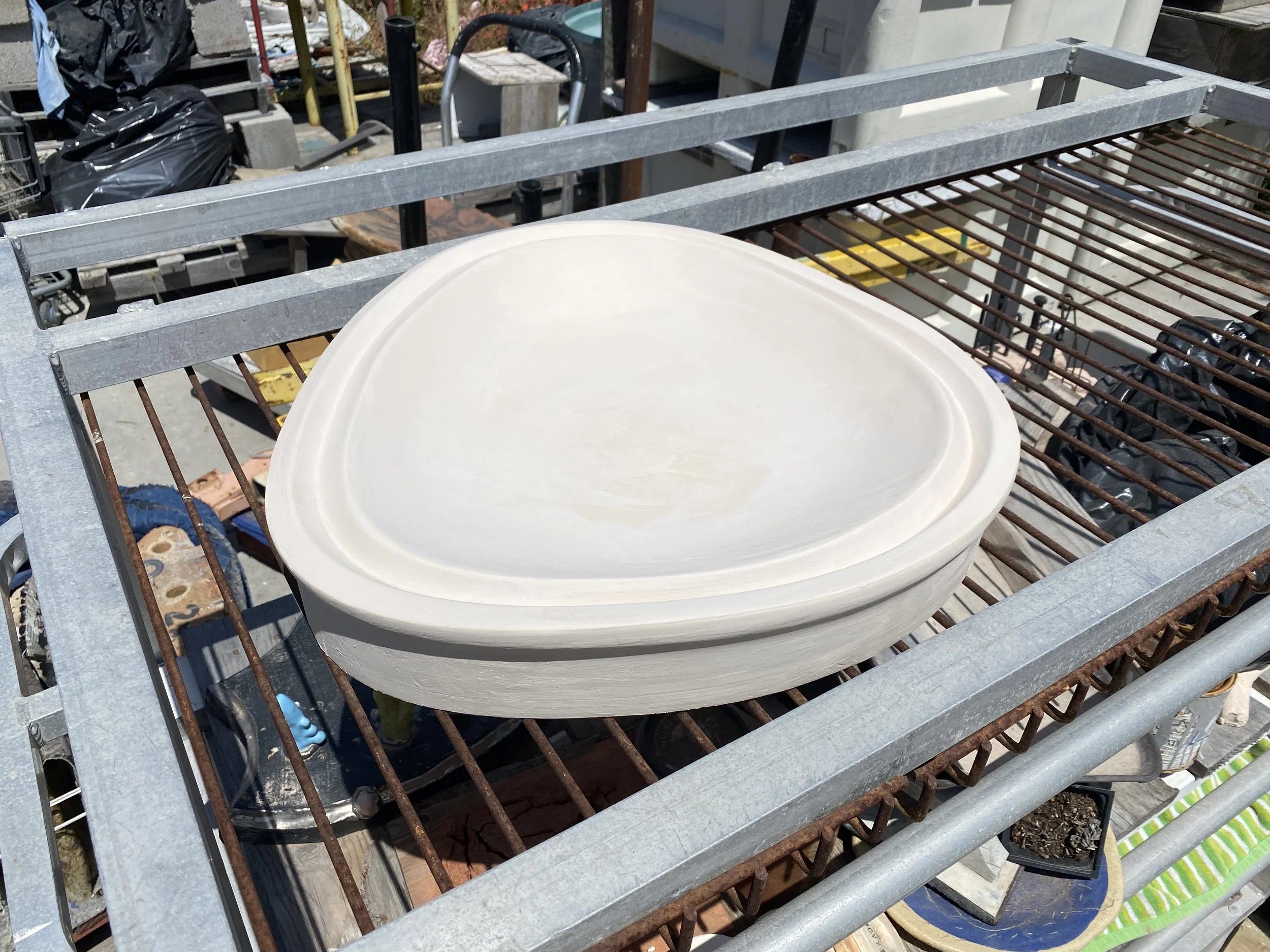
Glazing and Glaze Firing
A few snapshots from glaze selection, testing and final firing. We ended up with 10 good ones after it was all said and done! The best three were sent to you guys :-)



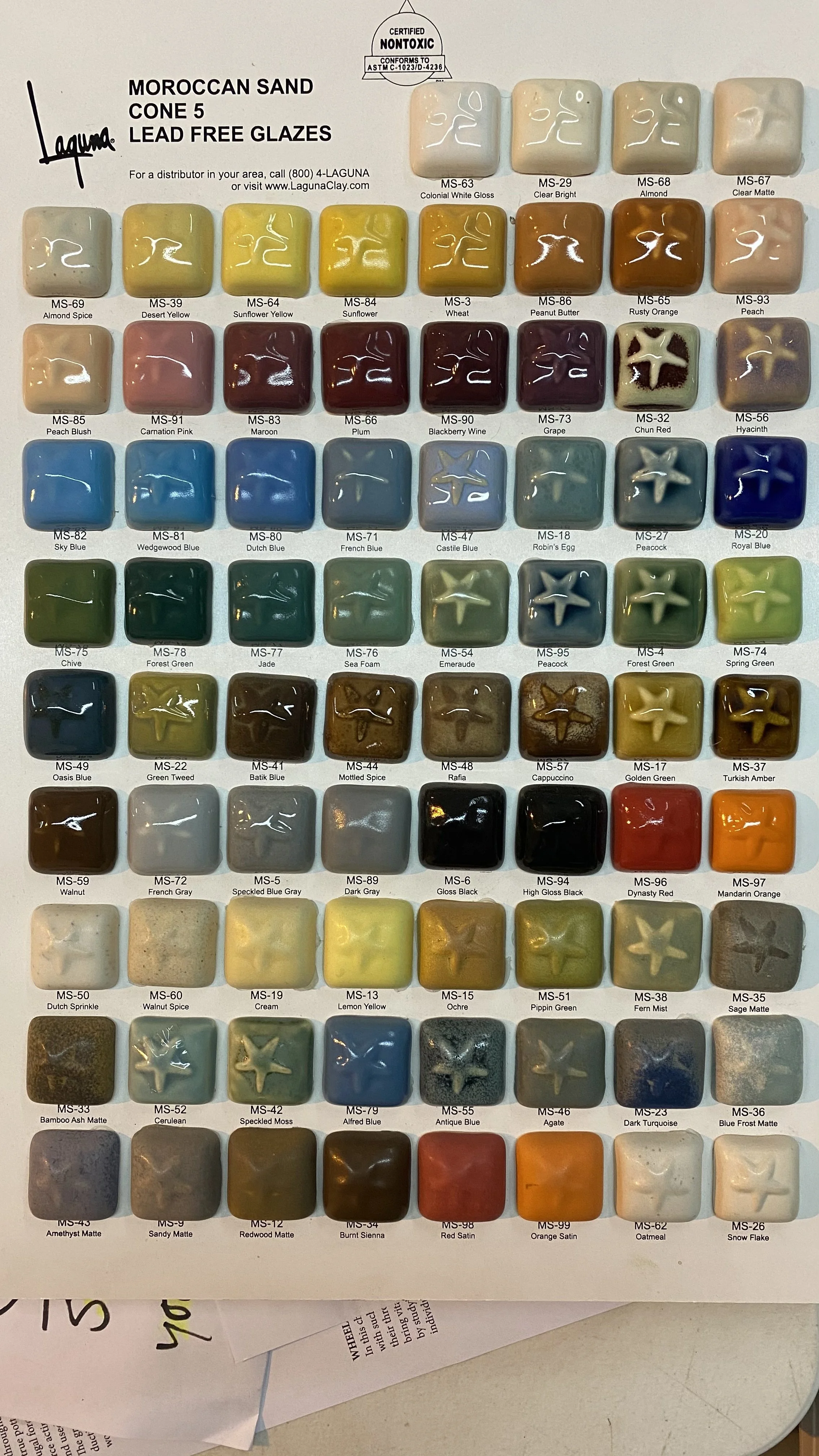

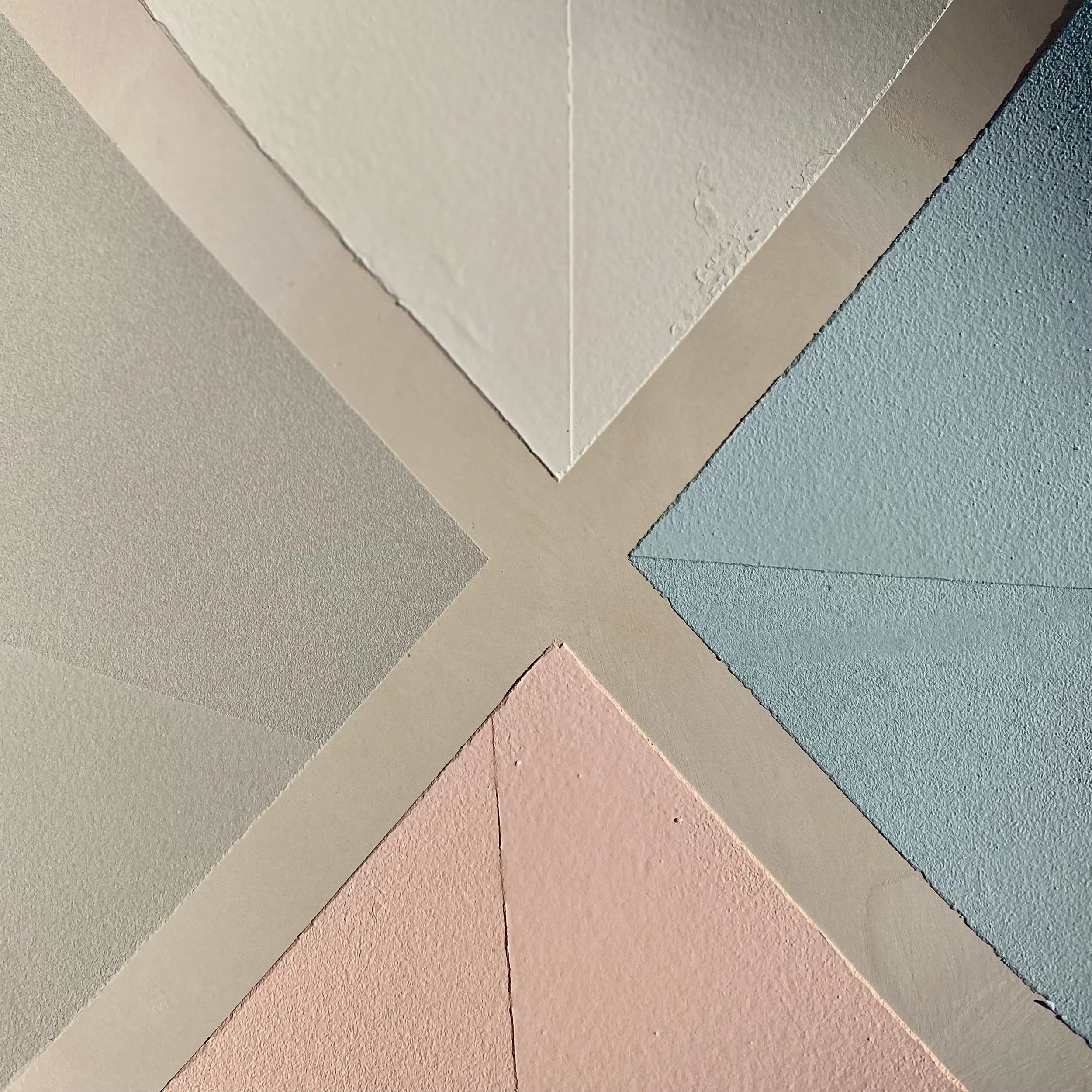


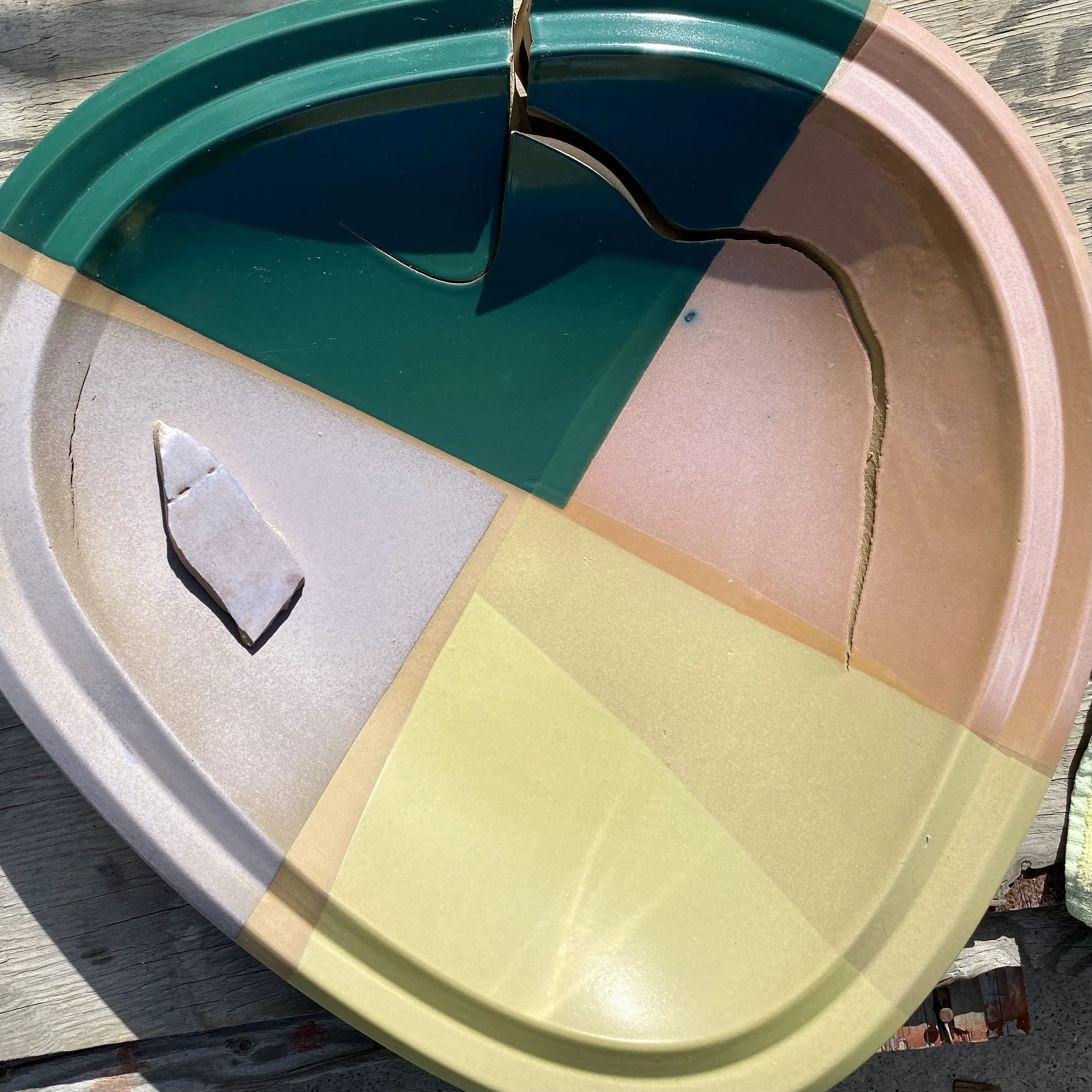
Packaging
To wrap everything up we wanted the final pieces to be delivered with intention, since these took so long we figured why not. Here’s a bit of the box design that Matt came up with.


